|
ACCESS THE FULL ARTICLE
No SPIE Account? Create one
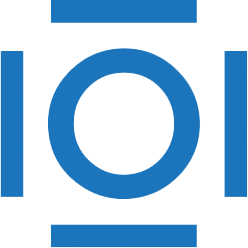
CITATIONS
Cited by 1 scholarly publication.
Silicon carbide
Plasma
Chemical species
Abrasives
Atmospheric plasma
Surface finishing
Optical fabrication