|
ACCESS THE FULL ARTICLE
No SPIE Account? Create one
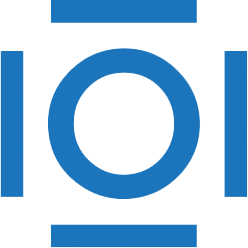
CITATIONS
Cited by 5 scholarly publications.
Sensors
Fiber Bragg gratings
Finite element methods
Fiber optics sensors
Optical fibers
Optical design
Environmental sensing