|
ACCESS THE FULL ARTICLE
No SPIE Account? Create one
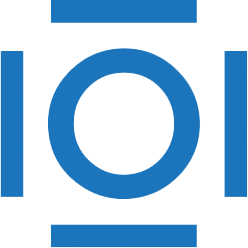
CITATIONS
Cited by 2 scholarly publications.
Finite element methods
3D modeling
Aircraft structures
Aluminum
Interfaces
X-ray diffraction
Mechanical engineering