|
ACCESS THE FULL ARTICLE
No SPIE Account? Create one
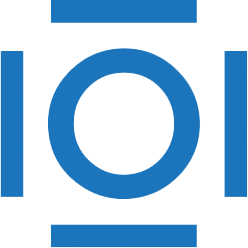
CITATIONS
Cited by 3 scholarly publications.
Mechanics
Microelectromechanical systems
Reliability
Analytical research
Beam analyzers
Coating
Deep reactive ion etching